ISO 9001 process mapping is a powerful tool that can help organizations improve their quality management systems. By visually depicting the flow of work, process mapping can identify areas for improvement, such as inefficiencies, bottlenecks, and unnecessary steps.
This article will provide an overview of ISO 9001 process mapping, including its benefits, steps, and tools. We will also discuss how to use process mapping to improve your organization's quality management system.
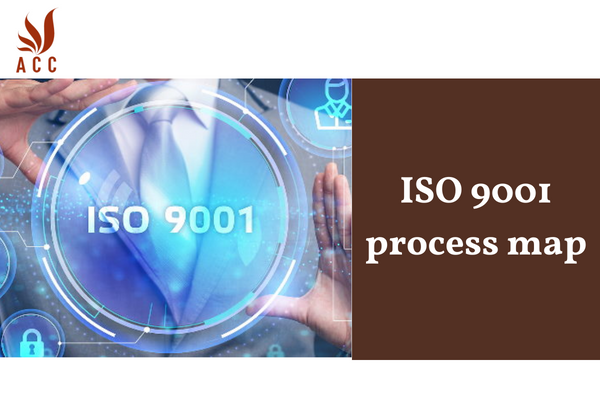
ISO 9001 process map
1. Introduction
ISO 9001 is an international standard that specifies requirements for a quality management system (QMS). A QMS is a set of processes and procedures that an organization uses to ensure that it meets the needs of its customers and other stakeholders.
Process mapping is a technique used to document and understand the flow of activities within a process. It is a valuable tool for organizations that are implementing or improving their QMS.
2. Benefits of Process Mapping
Process mapping can provide a number of benefits for organizations, including:
- Improved understanding of processes
- Identification of opportunities for improvement
- Increased efficiency and effectiveness
- Improved communication and collaboration
- Enhanced customer satisfaction
3. Steps in Process Mapping
The steps involved in process mapping are:
- Identify the process to be mapped.
- Gather data on the process. This can be done through interviews, observations, or document review.
- Create a draft process map.
- Review the draft process map with stakeholders.
- Finalize the process map.
4. Common Process Mappings in ISO 9001
There are a number of common process mappings that are used in ISO 9001. These include:
- Customer relationship management (CRM) process
- Product realization process
- Purchasing process
- Information management process
- Internal audit process
5. Conclusion
Process mapping is a valuable tool that can help organizations to improve their QMS. By following the steps outlined above, organizations can create process maps that are accurate, useful, and easy to understand.
Here are some additional tips for creating effective ISO 9001 process maps:
- Use clear and concise language.
- Use symbols and arrows to represent the flow of activities.
- Include all relevant information, including inputs, outputs, and decision points.
- Review the process map with stakeholders to ensure that it is accurate and complete.
6. Frequently asked questions
Nội dung bài viết:
Bình luận