1 Đánh giá nguy cơ cháy nổ trong quá trình chế biến gỗ
Nhận diện được những đặc điểm dễ gây nguy cơ cháy nổ trong quá trình chế biến gỗ, từ đó đưa ra các biện pháp phòng cháy chữa cháy đúng cách và đạt hiệu quả cao. Lưu đồ quy trình sản xuất chế biến gỗ
gắn ảnh
Từ sơ đồ trên có thể thấy nguyên liệu gỗ đưa vào xưởng được xẻ thành tấm theo kích thước xác định, sau khi xẻ thành tấm được đưa vào tẩm sấy để chống nứt, cong vênh. Gỗ sau khi sấy khô được vận chuyển đến phân xưởng chế biến chi tiết gồm phân xưởng mộc tay và mộc tay. Từ xưởng mộc bán thành phẩm được đưa về xưởng mộc làm thủ công những chi tiết mà xưởng mộc không làm được. Cuối cùng, bán thành phẩm này được chuyển đến phân xưởng lắp ráp và đánh bóng (sơn hoặc vecni), phân xưởng thành phẩm, sau khi được kiểm tra, đánh giá chất lượng sản phẩm và được chuyển đến kho Thành phẩm. * Quy trình sản xuất ván ép và các sản phẩm từ gỗ
Những khúc gỗ lớn được đưa vào máy bóc để xẻ thành những tấm dày từ 2 ÷ 3 mm. Sau đó được đưa vào máy sấy hơi nước ở nhiệt độ 100 độ C và áp suất hơi xấp xỉ 8,5 kG.cm2. Khi ra lò, các tấm ván gỗ này sẽ được chuyển sang bộ phận phủ keo phenolic và ép tạo thành các tấm theo kích thước đã định sẵn. Sản phẩm cuối cùng là ván ép. Đối với sản xuất diêm và bút chì, gỗ sau khi khô sẽ được đưa đến xưởng xẻ để cắt thành các hình dạng và kích thước định sẵn để sản xuất diêm và bút chì.
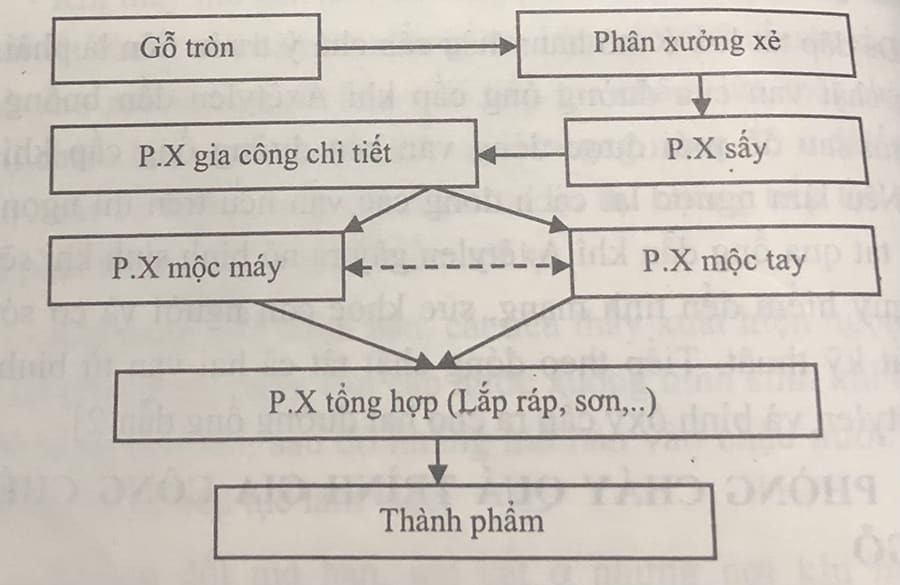
Quy định pccc xưởng gỗ
2 Đặc điểm nguy cơ cháy nổ trong cơ sở chế biến gỗ
dễ cháy
Trong quá trình chế biến gỗ (bao gồm các công đoạn: cưa, bào, tiện, phay, đánh bóng) tạo ra rất nhiều bụi và phoi bào, mùn cưa bay lơ lửng và tồn tại trong nền nhà xưởng nếu bám vào các bộ phận máy móc, cấu kiện nhà máy. . Nếu vật liệu gỗ càng chắc thì dăm, dăm, bụi càng nhỏ thì nguy cơ cháy nổ càng lớn. Bụi gỗ sinh ra khi máy móc làm việc, nhất là bụi sinh ra trong máy mài, đánh bóng gỗ có khả năng kết hợp với không khí tạo thành hỗn hợp nguy hiểm cháy nổ. Bụi gỗ trong không khí dễ tạo thành hỗn hợp nguy hiểm gây cháy nổ. Ví dụ, bụi gỗ từ 75 đến 100 μm có giới hạn cháy thấp (Cth = 12 – 25 g/m3). Trong quá trình chế biến gỗ, một số hóa chất, dung môi được sử dụng có nguy cơ cháy nổ bao gồm:
Sơn và vecni là chất lỏng có nguy cơ cháy nổ. Cồn công nghiệp (C2H5OH), axeton (CH3COCH3) tiềm ẩn nguy cơ cháy nổ. Các loại keo khác nhau, một số trong đó có nguy cơ cháy hoặc nổ. Sự tồn tại và phát sinh của nguồn lửa
Nguồn nhiệt gây cháy tại các xưởng mộc, xưởng gia công có thể do sự cố các thiết bị điện, vi phạm các quy tắc an toàn khi sử dụng điện. Có thể do ngọn lửa (trong trường hợp nhân viên không tuân thủ các quy tắc an toàn cháy nổ). Nhiệt sinh ra do ma sát (khi dầu, mỡ kém chất lượng; tốc độ của máy cao hơn quy định; máy bị quá tải và sự cố cần chú ý có thể do lắp lưỡi cưa, bào, v.v.) , xẻ không đúng chủng loại phù hợp với từng loại gỗ,…). Có thể do tia lửa điện sinh ra do va chạm giữa các mẫu kim loại rơi vào máy và cũng có thể do phoi cháy, mùn cưa trộn với dầu mỡ dùng làm chất bôi trơn khung cưa. . Khi điều tra nguyên nhân cháy trong quá trình chế biến, chế biến gỗ nhận thấy có nhiều nguyên nhân gây cháy nổ như:
Vi phạm nội quy PCCC (hút thuốc, đun nấu trong khu vực sản xuất). Vi phạm các quy định về hàn điện, hàn hơi hoặc sử dụng dụng cụ đốt keo điện hở. Vi phạm chế độ nhiệt độ khi sấy gỗ. Do không quan tâm theo dõi máy thường xuyên nên lâu ngày các thiết bị mô tơ hoạt động quá tải, các bạc đạn đỡ máy bị nóng gây chập cháy. Do sự va chạm của các vật rắn như cưa, dũa, sắt thép lẫn với gỗ sinh ra tia lửa điện làm bụi gỗ, mùn cưa bốc cháy. Hệ thống điện và các thiết bị nguy hiểm tại khu vực lò sấy cũng là một trong những nguyên nhân gây cháy gỗ. Ngoài ra, do dầu mỡ từ máy cưa rơi xuống sàn trộn với mùn cưa tạo thành hỗn hợp có thể bắt lửa, bốc cháy. khăn lau dầu và bụi; Mùn cưa, vỏ bào để lâu ngày phân hủy cũng có thể tự bốc cháy. Trong quá trình chế biến gỗ trong công nghiệp, nguồn nhiệt được sử dụng để làm khô gỗ. Quá trình sấy gỗ là một quá trình phức tạp, được đặc trưng bởi quá trình thất thoát hơi ẩm từ vật liệu ra môi trường sấy, sự truyền nhiệt thông bên trong vật liệu sấy và quá trình thoát hơi nước trên bề mặt vật liệu sấy và môi trường. Mức độ biến đổi độ ẩm của gỗ phụ thuộc vào nhóm, loại và kích thước của gỗ, v.v. Do đó, mỗi phương pháp sấy khô có mức độ nguy hiểm hỏa hoạn khác nhau. Hiện nay, 4 phương pháp sấy gỗ sau đây được sử dụng phổ biến:
phương pháp đầu tiên:
Sử dụng hơi nước nóng hoặc dùng khói và khí nóng đi vào các ống kim loại, các ống này được đặt cố định trong buồng sấy, các ống kim loại được truyền nhiệt bằng hơi nước hoặc không khí nóng vào buồng sấy, dưới tác dụng của không khí nóng, gỗ sẽ được sấy khô theo yêu cầu kỹ thuật. Các ống kim loại dẫn hơi nước, khói hoặc khí nóng có thể đặt bên dưới, bên trên hoặc hai bên buồng sấy. Nhiệt độ trong buồng sấy khoảng 80 độ C, còn nhiệt độ trong ống kim loại là 180 độ C, áp suất hơi khoảng 8,2 atm. Phương pháp sấy thứ hai: sử dụng khói và không khí nóng từ quá trình đốt cháy nhiên liệu, đồng thời dùng quạt thổi trực tiếp vào buồng sấy, ngoài ra còn thổi thêm không khí bên ngoài để lưu thông trong buồng và hút ẩm. Thời gian làm khô gỗ của cả hai phương pháp kéo dài liên tục từ một đến hai tuần. Phương pháp sấy thứ ba: Sử dụng điện cao tần. Phương pháp này rất hiệu quả, công suất cao, thời gian sấy chỉ từ 4-6 tiếng và gỗ khô đều, nhưng giá thành rất cao nên ngày nay ít được sử dụng. Nguồn điện được sử dụng để sấy lên đến 15.000 volt, khi đó nhiệt độ buồng sấy khoảng 100 độ C. ở 55-60 độ Xăng bắt đầu nóng chảy, ở nhiệt độ 100-120 độ C chuyển sang thể lỏng. Hạn chế nhiệt độ bắt lửa trên 250 độ C. Để sử dụng sấy gỗ, bạn chỉ cần cho xăng dầu vào thùng, sau đó đun nóng đến 140 độ C, bằng hơi nước nóng hoặc lửa mở hoặc điện. Sau đó, lần lượt cho các tấm ván có độ dày 4-6 cm vào thùng và tiếp tục sấy khô trong 10 giờ (sấy khô 1 m3 khối gỗ, dùng 20 kg dầu hỏa). Nguy cơ cháy khi sấy gỗ chủ yếu là do buồng sấy chứa nhiều củi khô và không khí vào buồng sấy chứa nhiều bụi dễ cháy. Do trên thành ống dẫn nhiệt có nhiều bụi bám với nhiệt độ sấy khá cao nên sau một thời gian bụi sẽ chuyển thành than và bốc cháy gây cháy buồng sấy. Trong bốn phương pháp sấy gỗ trên, nguy cơ cháy nguy hiểm nhất là:
Phương pháp dẫn khói và khí đốt nóng bằng nhiên liệu cứng vào buồng sấy. Trong trường hợp này, nếu đưa quá nhiều khí nóng vào, nhiệt độ sẽ tăng quá cao khiến gỗ bắt lửa và cháy buồng sấy. Trường hợp nhiệt độ khí, khói nóng trong ống kim loại vượt quá quy định, trên thành ống có nhiều cặn bẩn (mùn cưa, phoi bào, bụi,...) hoặc ống bị nứt, vỡ, khí nóng lọt vào ống dẫn đốt cháy gỗ. Phương pháp sấy bằng điện cũng có thể gây nguy cơ cháy nổ khi xuất hiện tia lửa điện do chập điện, phóng điện khi điện áp vượt quá mức quy định hoặc các tấm thép, gỗ không được siết chặt, tạo khe hở, sinh nhiệt cục bộ từng chỗ do độ ẩm không đều. Phương pháp làm khô bằng dầu hỏa lỏng tiềm ẩn nhiều nguy cơ cháy nổ vì xăng dầu có thể bắt lửa khi bó bị đổ hoặc để củi gần đáy và thành thùng cũng dẫn đến cháy. Khả năng lan truyền lửa
Xưởng sản xuất chứa đầy nguyên liệu gỗ, gỗ bán thành phẩm, dăm gỗ và bụi, mùn cưa sẽ là điều kiện để ngọn lửa lan nhanh. Để thu gom bụi, phoi bào, mùn cưa từ máy móc sản xuất, sử dụng máy hút bụi cục bộ và phương tiện vận chuyển khí nén. Đây là những điều kiện, khả năng cháy lan nhanh từ máy móc nào đó dọc theo đường ống công nghệ đến hệ thống giao thông chính của nhà máy.
3 Biện pháp phòng chống cháy nổ trong quá trình chế biến gỗ
Đối với các xưởng gia công, chế biến gỗ không loại trừ chất dễ cháy là gỗ với chất oxy hóa và không khí. Vì vậy, cần nâng cao các biện pháp phòng chống cháy nổ cho các quy trình công nghệ theo hướng ngăn ngừa sự phát sinh các nguồn nhiệt gây cháy, đồng thời loại bỏ lãng phí trong sản xuất, giảm khối lượng nguyên vật liệu, chuyển thành phẩm đến nơi bảo quản an toàn theo quy trình công nghệ. quá trình. Nhưng phải đảm bảo không làm giảm công suất của công nghệ sản xuất. Để chủ động làm tốt công tác PCCC tại các cơ sở này cần có kế hoạch, nội quy cụ thể và thực hiện các biện pháp sau:
Vệ sinh công nghiệp định kỳ cho từng phân xưởng, định kỳ 1 tháng vệ sinh hệ thống thông gió 2 lần. Luôn loại bỏ chất thải (mùn cưa, phoi bào, bụi) được tạo ra trong mỗi ca làm việc, sử dụng quạt hút và thông gió cục bộ thích hợp. Để đảm bảo không còn phế liệu lắng đọng, vận tốc không khí trong đường ống hút của máy không được chọn thấp hơn 15 (m/s). Rác: Dăm bào, mùn cưa trong nhà máy khi dùng để đốt lò hơi cần được chuyển trực tiếp qua ống dẫn khí vào chân không, sau đó chuyển vào lò đốt hoặc thùng làm bằng bê tông cốt thép, sau đó dùng quạt đưa vào lò đốt. lò vi sóng. Nếu gỗ phế liệu được chuyển đến lò đốt của lò hơi, các máy hút bụi, phế liệu sẽ được đặt gần lò hơi và gỗ vụn trước tiên phải được đưa qua buồng trung gian sau đó được chuyển đến buồng lò để đốt. . Không để nhiều nguyên liệu, sản phẩm gỗ trên bề mặt khu vực sản xuất quá lâu. Nếu có thể cơ giới hóa toàn bộ dây chuyền công nghệ từ dây chuyền sản xuất cục bộ đến dây chuyền sản xuất khép kín thì sẽ không còn kho trung gian để chứa gỗ trước và sau máy công cụ. Thường xuyên kiểm tra tình trạng hoạt động của các thiết bị điện và hệ thống sạc, nguồn. Không làm quá tải máy móc và động cơ. Thường xuyên kiểm tra nhiệt độ của các ổ trục, trục đỡ của máy. Nhớ tra đủ mỡ, đúng chủng loại, tránh trường hợp thiếu dầu bôi trơn làm nóng ổ bi và sinh nhiệt, gây cháy. Dưới những chỗ bôi mỡ nên có một cái hộp nhỏ để hứng đầu, để dầu không bị rò rỉ ra ngoài. Đối với động cơ điện hoặc các bộ phận truyền động, khi kiểm tra thấy nhiệt độ bề mặt vượt quá 150 độ C thì cần ngừng chảy và xem xét nguyên nhân để có biện pháp khắc phục kịp thời. Cần sử dụng lưỡi cưa sắc bén, lưỡi cưa cần mở các răng cần thiết theo thời gian đã định để khi làm việc không sinh ra ma sát đáng kể và tránh làm động cơ điện bị quá tải. Để đảm bảo răng cưa không bị gãy, độ mở tối đa của răng không vượt quá hai lần độ dày của lưỡi cưa, không sử dụng lưỡi cưa đã biến dạng. Không để các vật kim loại rơi vào máy cưa. Kiểm tra nguyên liệu gỗ trước khi đưa về xưởng gia công, nếu có đinh hoặc vật kim loại dính trên cây và tấm gỗ thì nên loại bỏ. Trong hệ thống thông gió và hút bụi phải sử dụng quạt có tác dụng bảo vệ chống tia lửa điện khi có va chạm. Ống thông gió phải có van, khóa tự động hoặc bằng tay (cơ học), nằm ở phần hút của động cơ, sau tấm lọc bụi. Máy hút bụi, phế liệu phải để ở phòng riêng, bên ngoài xưởng. Trong xưởng sản xuất, kho tàng phải có nội quy phòng cháy chữa cháy. Nghiêm cấm sử dụng lửa và đun nấu trong nhà máy. Chỉ định vị trí hút bên ngoài chu vi sản xuất. Tuyệt đối tôn trọng nội quy phòng cháy chữa cháy trong nhà máy (không hút thuốc lá, thuốc lá hookah, không sử dụng lửa trần, v.v.)
Thiết bị khởi động trong nhà máy gỗ phải là khởi động từ, không được dùng cầu dao làm thiết bị khởi động. Trong xưởng cưa và gia công các bộ phận (mộc), động cơ điện phải được trang bị vỏ bảo vệ để ngăn bụi gỗ, phoi bào và mùn cưa rơi xuống. Không làm nóng keo với các thiết bị điện mở. Có thể sử dụng các thiết bị gia nhiệt keo an toàn như hơi nước nóng, đèn và điện cực gia nhiệt. Khi bắn, keo chỉ được thực hiện trong buồng cách ly riêng. Tường và sàn phải làm bằng vật liệu không cháy. Cửa ngăn cách các phân xưởng sản xuất làm bằng vật liệu không cháy có giới hạn chịu lửa ít nhất là 0,75 giờ. Đối với buồng sấy cần được vệ sinh thường xuyên, không để phoi bào, mùn cưa, vỏ bào tồn đọng trong buồng sấy sau mỗi lần sấy và cả trước khi chuẩn bị đợt sấy mới. Các ống dẫn nhiệt phải được đặt cách vật liệu sấy gồm các ống nhẵn ít nhất 10 cm. Trên mặt ống phải có lưới bảo vệ bằng sắt để tránh gỗ vụn rơi xuống. Thường xuyên theo dõi, kiểm tra nhiệt độ không khí trong buồng sấy để đảm bảo nhiệt độ luôn ở mức 80 độ C, đồng thời kiểm tra áp suất hơi. Thường xuyên kiểm tra ống dẫn nhiệt không bị hở hay nứt, không khí bên ngoài được đưa vào đều đặn, lò phải đảm bảo đốt cháy hoàn toàn. Khi sấy bằng điện, các tấm gỗ phải được nén chặt không để có kẽ hở, gỗ phải cùng loại, cùng độ ẩm, dây dẫn điện và ấm kim loại phải cố định chắc chắn. Khi làm khô bằng dầu hỏa lỏng, đáy thùng phải dày hơn thành xung quanh, đáy thùng phải có lưới đặt cách đáy thùng 10-15 cm. Vaseline không nên đổ đầy mà nên cách miệng thùng sấy ít nhất 60cm để tránh bị đổ trong quá trình sấy.
Nội dung bài viết:
Bình luận